Bearing
Bearings are devices that limit the relative motion of a moving part, either rotating or translating, while reducing friction. Typically, when we mention bearings, mechanical bearings come to mind as they are the most commonly used type. However, bearings find extensive use across various industries such as machine design, automotive, transportation, oil & gas, and medical devices, essentially in any equipment that involves motion. In this note, I'll introduce magnetic bearings and explore their advantages over traditional mechanical bearings.Limitations of mechanical bearings
Mechanical bearings have a finite lifespan due to wear and tear and require regular lubrication. In high-speed applications, they may also necessitate specialized cooling systems. As consumable components, they need frequent replacement throughout the life of their parent device.
Magnetic bearing
A magnetic bearing performs the functions of a mechanical bearing using a configuration of permanent magnets. It consists of two sets of concentric magnetic arrays held in position by magnetic forces. Since there is no physical contact, magnetic bearings experience no wear and tear and typically have a very long lifespan. They can also handle high speeds and large loads without any friction. Consequently, magnetic bearings are increasingly favored in industries such as machine design, marine, automotive, aerospace, and medical devices. The rising popularity of magnetic bearings is evident across various sectors. Below, an image shows an axial magnetic bearing where the outer bearing is stationary and the inner bearing, attached to a spinning shaft, is levitated by magnetic forces supporting the shaft's weight.
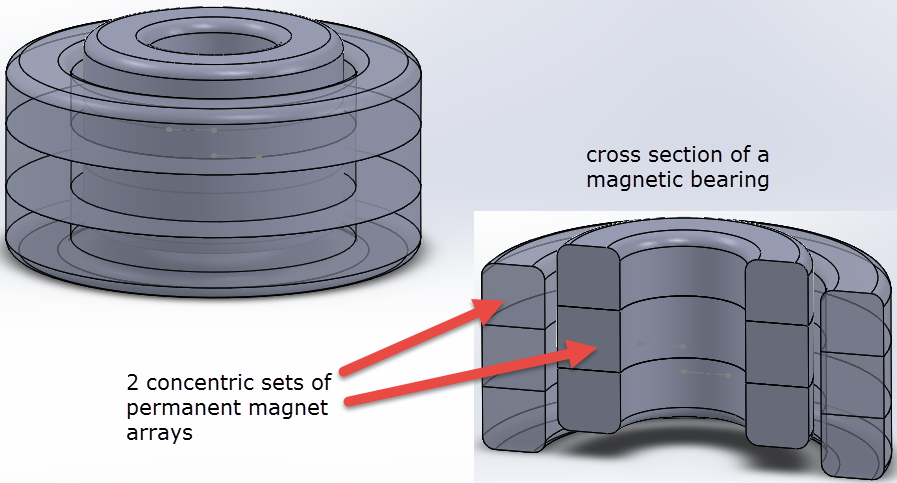
A magnetic bearing design simulated using EMS
EMS assists bearing designers in sizing their magnetic arrays to accommodate various shaft designs and weights, ensuring optimal performance. Another advantage of magnetic bearings is their ability to support the offset of the inner cylindrical array relative to the stationary outer cylinder. This flexibility enhances the functionality and adaptability of magnetic bearings in diverse applications.
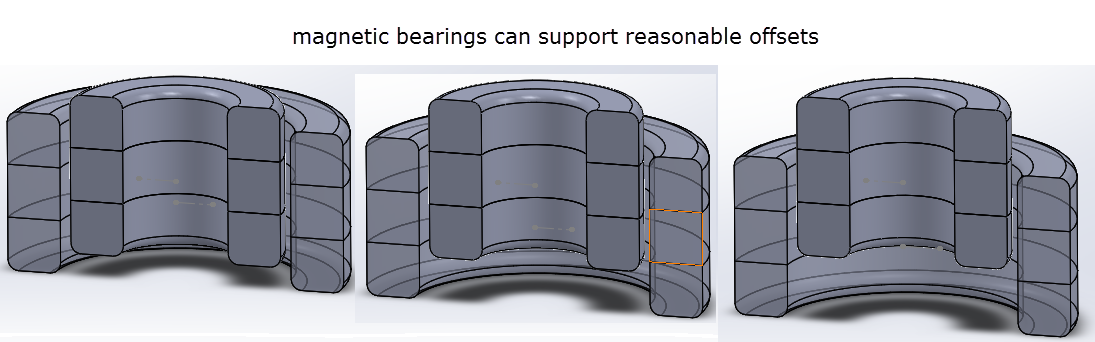
EMS software provides precise predictions of the forces acting on the inner bearing across different offset positions. The magnetic arrangement is depicted in the accompanying figure, with the N-S direction of each magnet indicated by black arrows. This configuration can be efficiently modeled in EMS, allowing for the visualization of magnetic flux distribution and the calculation of axial forces acting on the inner array. This capability is crucial for optimizing design and ensuring the functionality and reliability of magnetic bearings in various applications.
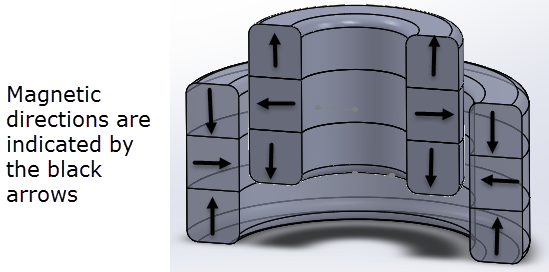
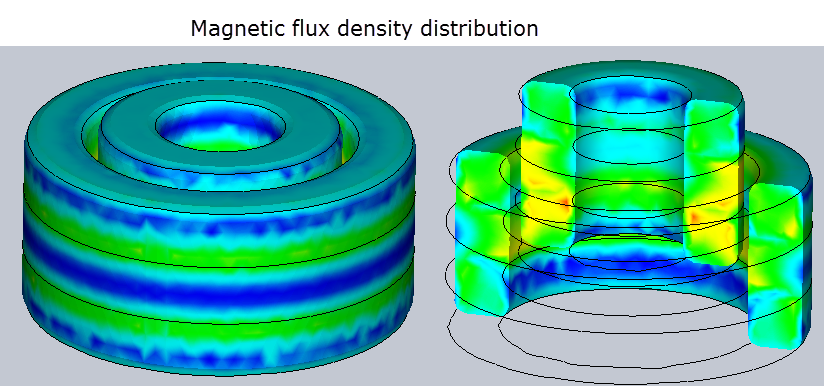
The variation of axial force acting on the inner magnet array with the offset is automatically computed by EMS, as illustrated below. It's important to note that the axial force increases with the offset distance, but after reaching a certain point, the force begins to decrease. When the offset exceeds 18 mm, the force reverses direction, effectively pulling back the inner array. Utilizing these axial force values, engineers can calculate the axial magnetic stiffness coefficient, an essential parameter for optimizing the stability and performance of magnetic bearing systems.
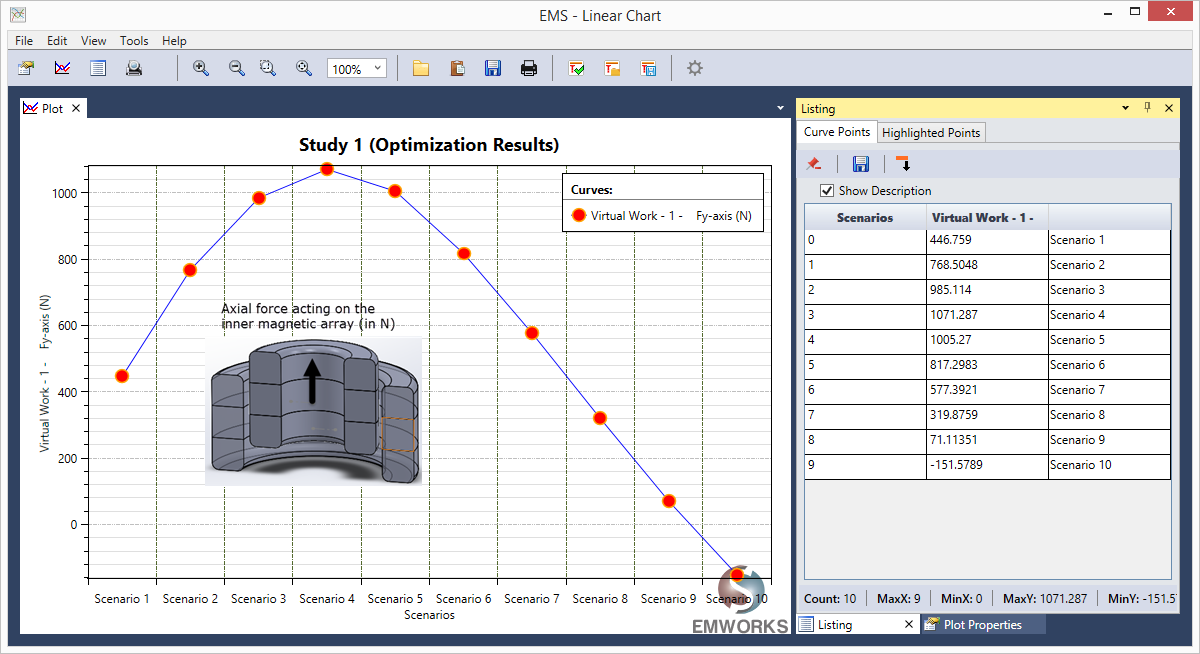
Conclusion
Magnetic bearings represent a significant advancement over traditional mechanical bearings, offering enhanced performance and longevity. By eliminating physical contact, they reduce wear and tear, operate without friction, and can handle higher speeds and loads. This translates to lower maintenance costs and longer service intervals. With the aid of EMS simulation software, engineers can precisely design and optimize these bearings for various applications, from aerospace to healthcare. As the adoption of magnetic bearings increases, they are set to redefine standards in machinery design, providing a reliable and efficient solution that meets the modern demands of industry.