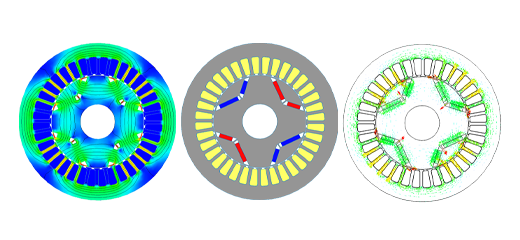
In recent years, interior permanent magnet (IPM) motors have received much attention and have been used in many applications, including electric vehicles (EVs), electric aircraft and helicopters, marine propulsions, and aerospace applications. However, most of the IPM motor designs have symmetrical rotor structures, causing the PM and reluctance torque components to reach their maximum at different current phase angles. Consequently, the motor can only utilize a portion of its individual torque components. Therefore, the “Asymmetric design approach” can be considered as a new potential solution to reach better torque performance. In contrast with conventional symmetrical design, an asymmetric IPM (AIPM) motor can produce a higher average torque while the torque ripple rate can be reduced. In this regard, motor designers have shown a great interest in investigating possible applications of AIPM motors using methods such as finite element analysis (FEA).
In this webinar, we shall discuss examples of symmetric and asymmetrical rotor structures and their concepts. Then, we will dive into the FEA-based simulation analysis using EMWorks electromagnetic simulation software. Finally, a comparison between the asymmetrical rotor with the conventional symmetrical rotor design for the IPM motor will be performed under the same operating condition.
In this webinar, we shall discuss examples of symmetric and asymmetrical rotor structures and their concepts. Then, we will dive into the FEA-based simulation analysis using EMWorks electromagnetic simulation software. Finally, a comparison between the asymmetrical rotor with the conventional symmetrical rotor design for the IPM motor will be performed under the same operating condition.